Growing bamboo can be a fun and satisfying hobby. But if you’re cultivating bamboo on a large scale, then you probably want more than just fun in the sun. You need a way to monetize it. We all know that bamboo has an enormous range of practical, commercial uses. And with the right machinery, you can turn your timber grass into flooring, toothpicks, chopsticks, biofuel, toilet paper, charcoal, and hundreds of other products. But to make these wares, you need the right equipment.
Machinery for processing bamboo is available in a wide variety of models. You can split your bamboo into sticks and skewers, laminate it into a high-quality building material, cook it into charcoal, or reduce it down to pulp. These machines are not only for major producers with thousands of acres of bamboo. Smaller farmers with more modest operations can also make use of this machinery, allowing them to get more from their crop and convert their canes into more useful commodities.
Bamboo factories and processing facilities
Until quite recently, a bamboo grower needed to have a vast plantation in order to make bamboo processing a viable option. With anything less than about 5,000 acres, it simply wasn’t worth it to build a factory that could turn that woody grass into paper or flooring.
Some of this kind of industrial machinery can process many tons of bamboo each day. And such a significant investment doesn’t really pencil out unless the equipment is running at full capacity, or something pretty close to it.
The scenario has led to something of a chicken-and-egg dilemma for bamboo producers in places like Europe and the United States. These Western regions are eager to establish their own bamboo farming and manufacturing. Among other reasons, they’d like to stop shipping the raw material and the finished goods all the way from Asia.
But without adequate acreage of bamboo plantations, building a local factory seems like a risky business. At the same time, without factories and processing facilities for bamboo, farmers are hesitant to raise a plantation of this otherwise promising crop. The vast majority of bamboo mills and factories are still in China.
Without equipment nearby to process the bamboo, farmers will be looking at a massive stockpile of woody poles. Beautiful and elegant though bamboo may be, those long poles can be prohibitively cumbersome when it comes time to ship and deliver.
There’s a certain amount of demand for raw bamboo poles for art installations and rustic construction projects. But you can only build so many gazebos. Eventually, bamboo producers need a way to turn their harvest into something more moveable and marketable.
Practical options for bamboo processing
The good news is that you don’t necessarily need to build your own bamboo factory or live within 100 miles of one to make bamboo farming worthwhile. Small and medium-sized bamboo farmers in the United States, Africa, and even Southeast Asia can find specialized equipment to turn their woody grass into a commodity.
The type of machinery they decide to invest in will depend primarily on their geographic location and the varieties of bamboo they’re cultivating.
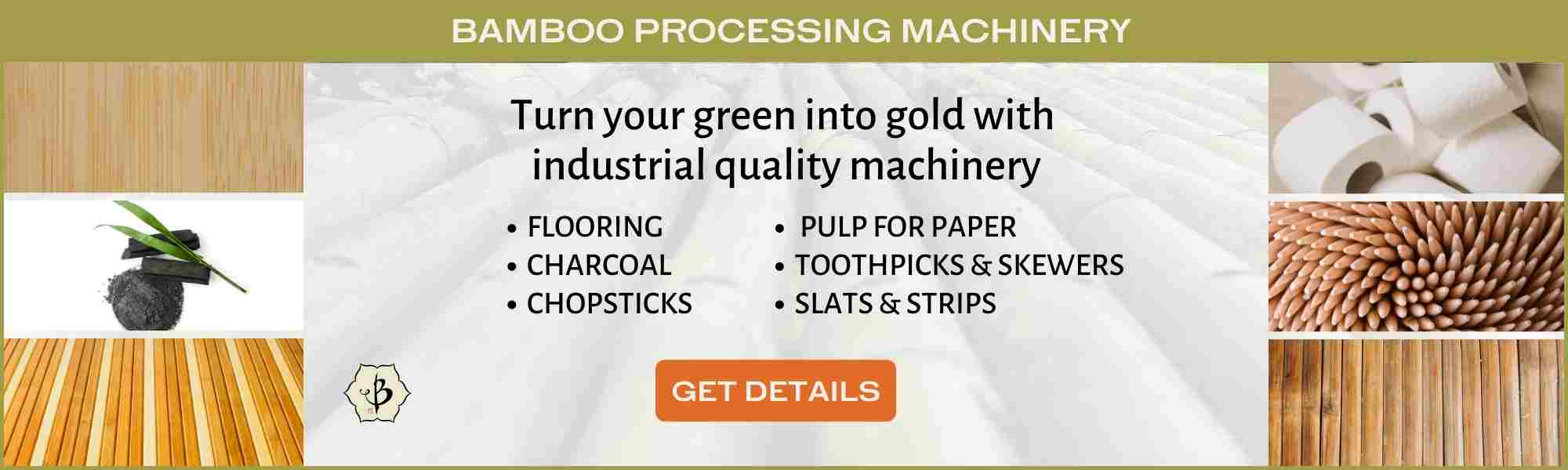
BAMBOO CHARCOAL
Machines that turn bamboo culms and remnants into charcoal, or biochar, are among the most popular options. Any factory that’s making something out of bamboo will end up with lots of leftover scraps and sawdust. And every bamboo farm will end up with a certain quantity of lesser quality poles. Rather than let those byproducts go to waste, why not turn them into charcoal?
In order to perform the complete process, the system includes a total of four different units. The standard set up can process around 400 kilos of raw bamboo per hour. The system is simple to operate and maintain, and costs less than $20,000 altogether. (Overseas shipping not included.) More expensive and elaborate equipment can perform the pyrolysis conversion even faster.
While very useful in a factory setting, these are also relatively affordable machines for smaller-scale producers. And the bamboo biochar itself has quite an array of uses.
Farmers will find that plowing the charcoal back into the earth can do wonders for the soil. It can raise the soil pH (reducing acidity) and generally increase the soil’s productivity. This is an attractive prospect for growers seeking higher yields, and also for reforestation projects that aim to restore degraded landscapes.
In Africa, the site of many new bamboo plantations, charcoal is still the most widely used resource for cooking and heating homes. The felling of trees for charcoal is a major contributor to Africa’s high rates of deforestation. And the traditional methods of charcoal production, with earth pits and fire, are terribly inefficient and polluting. Bamboo charcoal is much cleaner to produce, especially when using the right machinery.
Bamboo charcoal also works well for water filtration and air purification. It has an amazing capacity to filter toxins from the environment.
(See our in-depth articles on Bamboo Charcoal and Bamboo in Kenya.)
BAMBOO PULP FOR PAPER
In India and other parts of Asia, they commonly use bamboo for making paper. It’s a traditional practice and a desirable alternative to cutting down trees. The process is also milder than the chemically intensive methods for pulping trees.
More recently, the interest in bamboo toilet paper has surged, especially in the US. The sad truth — that we’ve been cutting down virgin, old-growth forests to make the softest bathroom tissue — is finally coming to light, and consumers are clambering for a more sensible alternative.
Bamboo pulp can also be spun into yarn or made into biodegradable packaging products, like an eco-friendly alternative to styrofoam.
A few different pieces of equipment are needed to turn woody bamboo into pulp. From there, you can sell the pulp, or use additional machinery to turn it into a more finished product, such as yarn or paper.
TOOTHPICKS & CHOPSTICKS
Some species of bamboo produce smaller poles, not so suitable for construction or for engineered lumber. And even the best quality timber bamboo will occasionally produce some inferior stalks.
For these instances, the smaller canes can easily be made into things like toothpicks, skewers, chopsticks, or incense sticks. Producing these items involves a pretty straightforward process with just a small line of equipment.
After the first stages of processing are complete, the production line branches off to make the specifically sized sticks. Most factories, therefore, will end up installing the setups for at least two different end products, e.g. toothpicks and incense sticks.
The equipment for one product will cost between $15-$20,000. But just a few thousand more will enable you to produce a couple of different end products.
LAMINATED BAMBOO & STRAND WOVEN BAMBOO LUMBER
The most sophisticated bamboo factories and facilities are turning their top-quality timber bamboo — be it Moso, Guadua, or Asper — into flooring or engineered lumber.
Lamination machinery presses layers of bamboo together, suitable for flooring, cabinetry, and other finishing pieces for carpentry. The sheets of laminated bamboo, or parquet, can also be shaped into cutting boards, kitchen wares, and all manner of accessory items.
This processing requires a larger factory space for a complete setup with more than 20 pieces of equipment. Specific machinery and configurations will depend on the desired output. It’s also possible to start with a smaller setup and then upgrade with a couple more units in order to ramp up the pace of production and output.
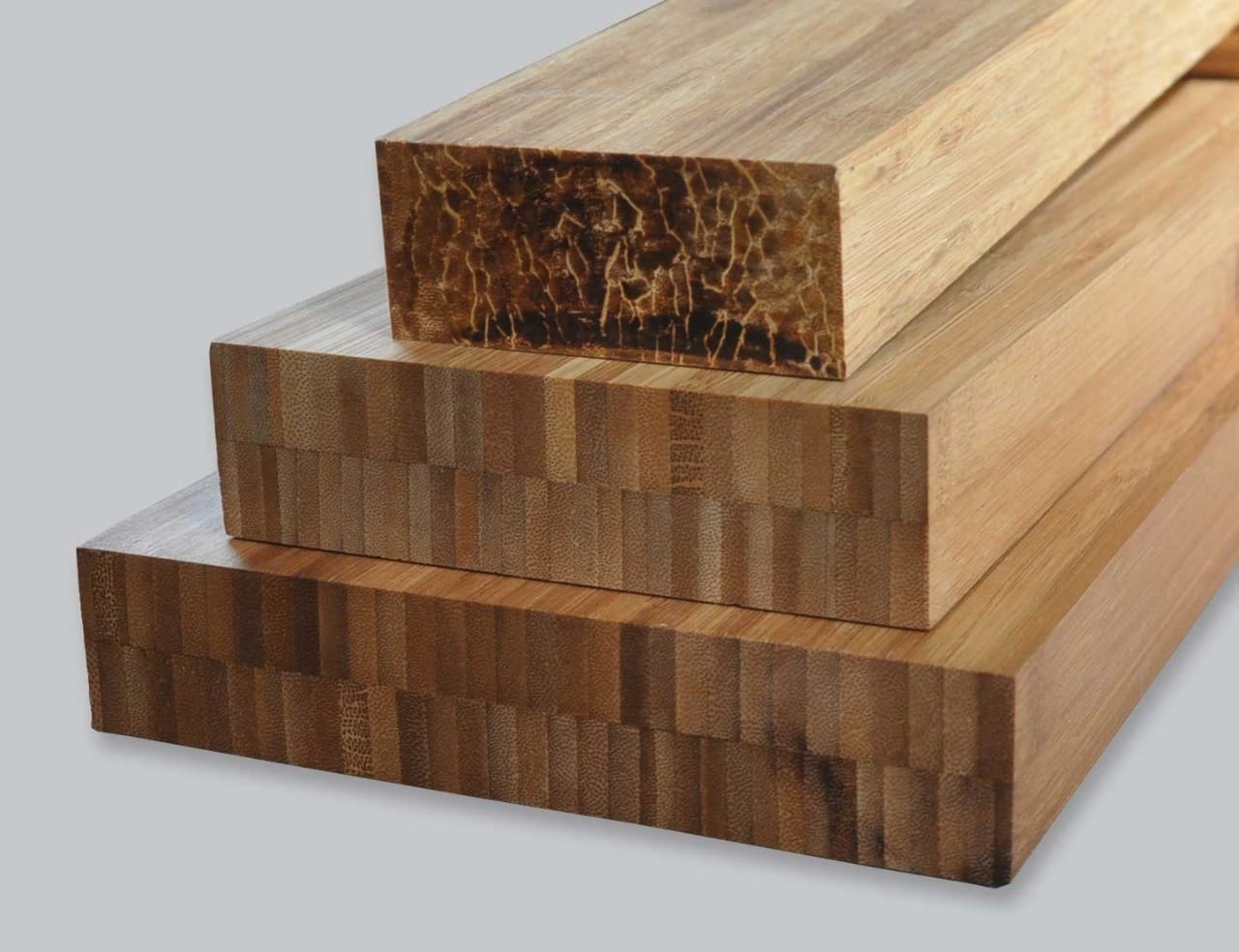
For the highest-quality bamboo building material, upscale manufacturers are using the strand woven process. This method crushes and compresses the bamboo with 3,000 metric tons of pressure. The end result is some extraordinarily hard lumber, with a beautiful wood-like grain. This material makes the hardest flooring, stunning furniture, and is even suitable for exterior use, like decks, capable of withstanding the outdoor elements. And strand woven lumber sells for at least 40% more than the traditional bamboo laminate.
For these more elaborate manufacturing installations, a technician will fly to your factory and stay for a month to oversee the setup and train the factory workers on the proper use and maintenance of the machinery.
The complete machinery for the bamboo laminate process runs between $275K and $325K. The strand woven lumber processing equipment can cost anywhere from $800K up to 2 or 3 million. These prices include one month of onsite installation and training, but not overseas freight costs.
Check out our articles on Strand Woven Bamboo and The Future of Bamboo Construction to learn more.
Looking for more
For more details about the processes and equipment used in bamboo manufacturing, feel feel to contact us directly. You can also peruse our website to learn more about the properties and benefits of bamboo as a renewable resource and a sustainable building material. And don’t miss our article on Raw materials and the bamboo supply chain.
I want to know how to make the colour of pulp white
A bleaching process is required
Greetings, I am from Papua New Guinea and we have a number of bamboo species that grows naturally on our land.
Would appreciate partnership approach to venture in to this exciting industry.
I am interested in setting up bamboo industry in Africa. Can you give more technical advise on how best to go into it. I want to know what size of land needed for bamboo farm to sustain the factory. I would like to produce all bamboo products from toothpicks to strand woven lumbers.
Thank you sir.
Yes, it can be done on a smaller budget for products like toothpicks. Strand woven lumber production will require at least 500 hectares to be practical. Email me if you’re interested in sourcing the equipment.
Hi, my name is Windsor from Indonesia. I would like to ask if you have any knowledge of the specific mechanization of bamboo harvesting for pulp. thank you
Please send me a private message.
Hi,
For a while I am looking into establishing a bamboo plantation. I am based in Kosovo ,Southeast Europe, with a typical continental climate, hot summers and cold winters. Currently I am looking to expand my options and additionally researching into processing options once a plantation is set. Would be very interested to hear from you about variety of the bamboo you would recommend and the processing potential at later stages.
Look forward hearing from you.
Regards,
Very interesting. Please email me.