The idea of bamboo construction probably dates back as far as writing on stone tablets. But the most modern bamboo buildings look nothing like the rustic structures of the past, just as the tablets of Gilgamesh bear little resemblance to the tablets we now use to make Zoom calls and watch Youtube. At Virginia Tech, however, Industrial Design Professor Jonas Hauptman is bringing together the best of both worlds, with a building material he calls Smart Bamboo.
Smart Bamboo is unlike any other bamboo building material. This structural composite manages to form regular, standardized panels, suitable for large-scale construction, without having to disassemble the bamboo from its natural state and then glue it back together.
Smart Bamboo and the evolution of bamboo engineering
For centuries, Asian architects have appreciated the strength and versatility of bamboo, using the sturdy poles to build houses, bridges, furniture and scaffolding. The woody grass lends itself well to all manner of crafts and carpentry. Traditional bamboo architecture has a rustic charm that showcases the plant’s smooth curves and natural aesthetics.
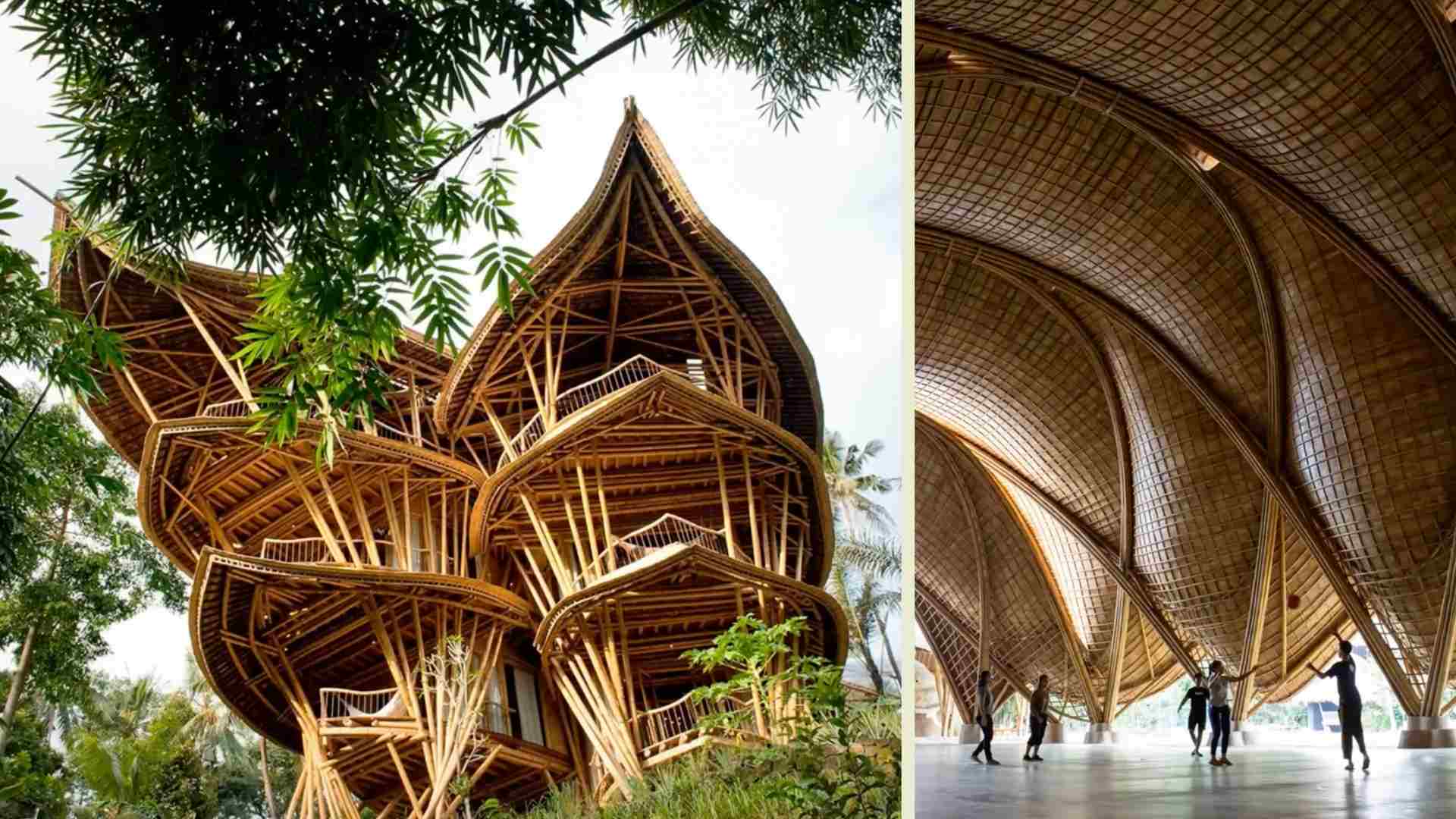
In recent decades, modern designers and engineers have rediscovered the beauty and utility of bamboo construction. And today you can find towering bamboo temples, theaters and resorts punctuating the landscapes in various tropical settings from Colombia to Sri Lanka. Still, the natural variation in these sleek poles makes a material that’s somewhat unpredictable and not reliable for standardization. Instead, it’s better suited for outdoor, open-air pavilions and other one-of-a-kind structures.
At the other end of the bamboo building industry, modern techniques and technology have paved the way for engineered bamboo beams and panels, typically comprised of individual strips laminated together in standard dimensions. The regularity of this kind of material is perfectly suited for large-scale construction that can be easily replicated. However, this consistency comes at the cost of having to split the poles into narrow strips and process them with heavy machinery and industrial adhesives.
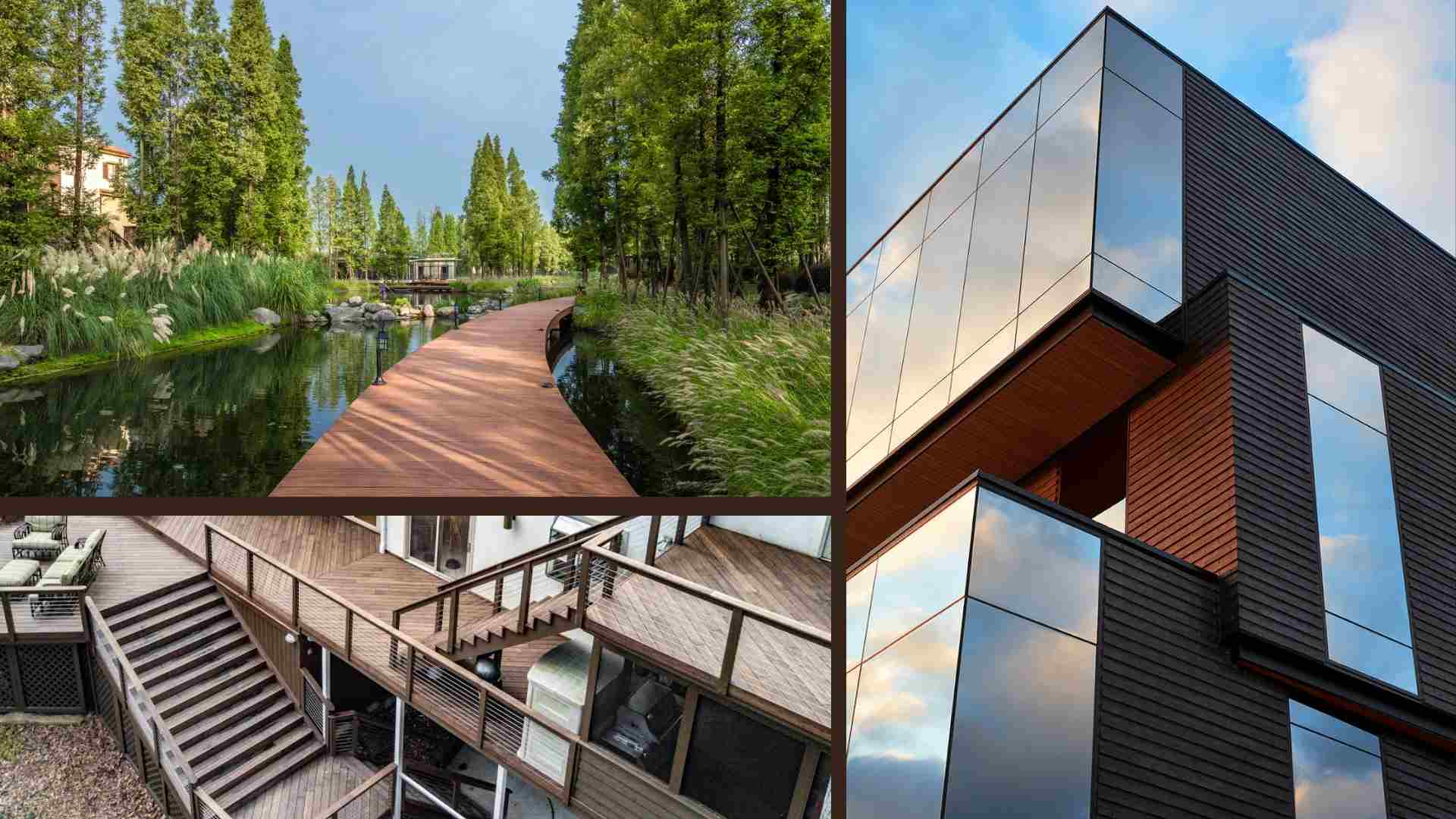
The most modern of such designs, coming from bamboo vanguards like Dasso, Moso, Renuteq, and Lamboo, achieve unmatched levels of elegance. But the casual observer would scarcely recognize these versatile materials as being derived from bamboo.
Smart Bamboo takes the best of both worlds
While bamboo construction generally consists of either raw poles arranged with delicate precision, or else dismembered bamboo fibers systematically laminated and compressed into beams and planks, Smart Bamboo offers a brand new approach. Hauptman and his team, Daniel Hindman, Keith Hack, and Greg Marggraf, have devised a unique innovation that is a composite, but one consisting of whole bamboo poles. (Check out their peer-reviewed paper for complete details.)
Rather than splitting massive timber bamboo into thin, narrow strips, they take nearly solid bamboo varieties and plane the rounded sides to make them flat. The squared-off poles are then arranged side by side in parallel. Additional layers of thinner poles, also squared and flattened, run perpendicular. The result is a thick panel with tremendous structural strength in all three directions.
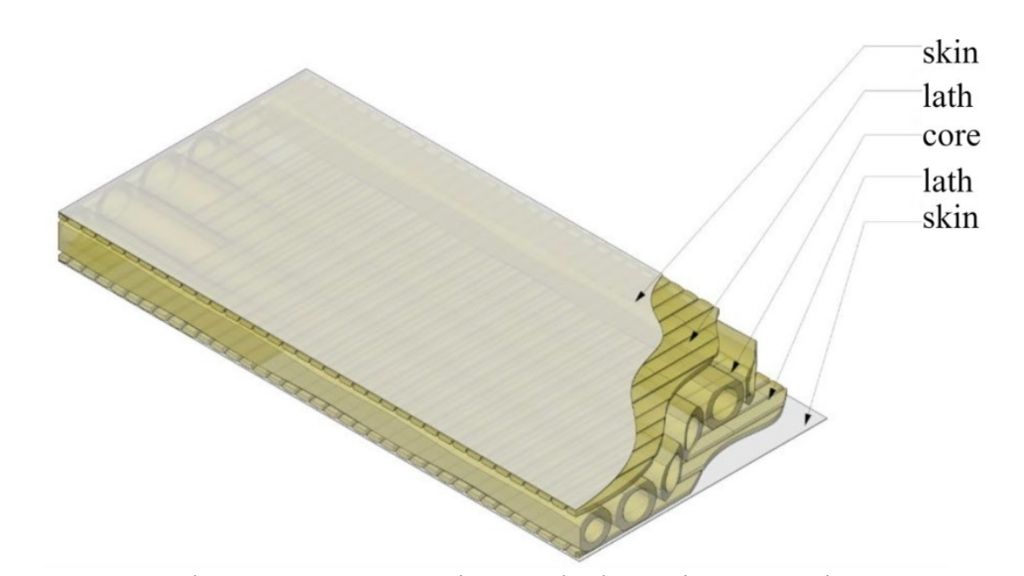
To prove the fortitude of this material, the crew at Virginia Tech has subjected its prototype panels to enormous stress from all sides. (See the featured image at the top of this article.) Lengthy experimentation and steady refinements have led them to what they deem the optimal arrangement of bamboo pieces.
Also, because they are not laminating the bamboo into solid boards, an integral part of their design strategy has been to use solid or the most nearly solid species of bamboo. Unfortunately, there continues to be some lack of academic consensus on the names and taxonomy of these Asian grasses, but some of their preferred varieties include Dendrocalamus strictus and Tre Gai from Southeast Asia, and certain species of Guadau and Chusquea from South America.
The unusually thick walls of these bamboo types allow the design team to shave a bit off the sides to make them squarish without compromising the poles’ strength. Still, there are hollow spaces and cavities, which reduce the overall weight of each panel and provide some natural insulation properties. But ultimately, there’s far less waste than with most other bamboo composite methods.
Forward-thinking with Smart Bamboo panels
With so many varieties of bamboo material already on the market, why were Hauptman and his colleagues so interested in developing another innovation?
The primary goal of Smart Bamboo is to address the growing housing crisis in the developing world without deepening the already severe climate crisis. Standard construction materials like concrete, steel and aluminum are responsible for nearly half of the greenhouse gasses emitted into the atmosphere each year. But as the populations continue to rise in the Global South, the need for affordable, low-carbon housing solutions is intensifying.
The same parts of the world where these housing issues are most pressing are, by and large, the same areas where giant timber bamboo grows most prolifically. It only makes sense then to make better use of this abundant resource. Increased reliance on bamboo reduces the need to cut down trees or produce concrete. At the same time, bamboo cultivation is a powerful method for generating oxygen and sequestering atmospheric carbon.
Hauptman and his team are currently in early talks with organizations in the Philippines, Vietnam, Indonesia, Columbia, Nepal, Kenya, Guatemala and other parts of the tropical world, hoping to build affordable homes and fruitful partnerships. We wish them all the best and will be watching them closely.
To contact the Virginia Tech bamboo research and development team, please visit their website.
Get smart
If you’re interested in learning more about bamboo building, check out some of our related articles about innovative projects taking place all over the world.
FEATURE IMAGE: 3-point bend testing. Photo courtesy of Hauptman, et al at Virginia Tech.
What kind of joinery system Is going to be used?
Final offer of panel dimensión?
Wright per M2 of paneling
These composite materials are still in the R&D phase, and they are exploring a varieties of methods and joinery techniques.